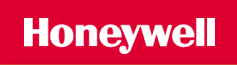
DCP250 is a microprocessor-based 1/4 DIN size panel mounted controller and programmer. It is used for temperature and process control of industrial ovens, furnaces, environmental chambers, sterilizers, boilers, steam processes, food & beverage and packaging processes. Single or dual loop control, combined with real-time clock timer, profiler, data logging and trending capabilities, provides good control performance and flexibility for batch process profiling needs.
What Is It?
?The DCP250 is a flexible and powerful instrument that supports one or two control loops and profiling with 255 segments that are shared in 64 programs. It also provides easy access to data and simplified user operation with a graphical text display, device configuration file upload and download as well as data log file extraction via USB port, and direct access for programming with its top of the instrument connection port interface to a PC.
How Does It Work?
?The DCP250 controller and programmer uses microprocessor technology to convert an analog input signal (i.e. temperature, flow, pressure) into digital data, which is then compared to a desired set point value established by the user. It has internal algorithms that drive an output signal (based on the error of the input from the desired set point) to a relay or analog output that controls the process equipment, which can impact the measured analog input.
Instrument configuration, set-up and operation can be performed via an integral keyboard and display. The DCP250 also supports internal memory that is used for data storage and replay via the display. These stored data files can also be extracted from the instrument via a USB port.
What Problems Does It Solve?
?DCP250 helps users efficiently manage and optimize their temperature and process control applications. Benefits include accurate control, the ability to run a variety of time versus temperature profiles, automated data storage and retrieval, and easy user operation. It also stores and displays the relevant process data that can be used to manage and optimize product quality.
|